Introduced in 1954, the Mercedes-Benz 300SL captivated enthusiasts with its sleek design and powerful race-bred engine. However, its most groundbreaking feature was hidden beneath its curvaceous bodywork. This innovative tubular space frame chassis transformed automotive engineering.
Racing Roots and Pioneering Vision
The 300SL’s origins trace back to Mercedes’ post-war ambitions to return to international motorsport. Rudolf Uhlenhaut, a gifted engineer and racing driver, was tasked with transforming the company’s successful W194 race car into a production sports car. With limited resources, unconventional solutions were required.
Uhlenhaut’s team found inspiration in lightweight tubular frames used in aircraft design. They created an incredibly rigid yet featherweight chassis weighing just 82kg by welding thin-walled steel tubing into a triangulated lattice structure.
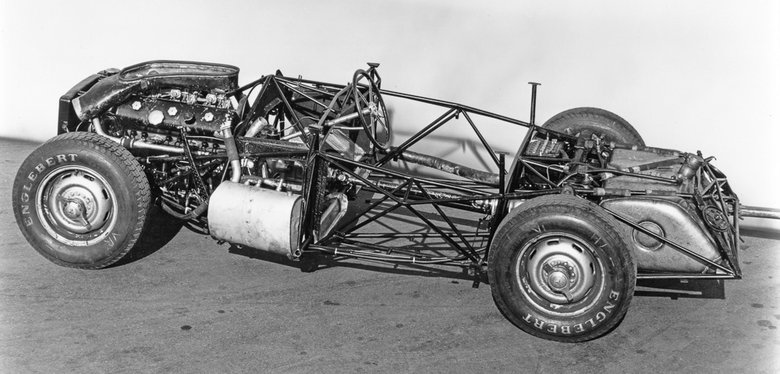
Designing the Groundbreaking Tubular Frame
The development of this groundbreaking chassis presented the Mercedes team with a range of complex engineering obstacles. They had to meticulously fine-tune the triangulated geometry and tube gauges to achieve the perfect equilibrium between rigidity and weight. To accomplish this, they utilised the most advanced high-strength, lightweight tubing available and implemented specialised welding techniques to create robust connections between the tubes.
The triangulated design effectively distributed loads in both tension and compression along the entire length of the tube members, fully harnessing the material’s inherent strength. This highly efficient approach ultimately led to the creation of a chassis that was significantly stiffer and lighter than existing designs of the time.
Innovative Engineering Solutions
To minimise frontal area and improve aerodynamics, the frame’s front section was made extremely low and narrow, with the engine tilted at a 45-degree angle. A dry-sump lubrication system prevented oil starvation during high-G cornering.
The tubular space frame enabled the 300SL to achieve spectacular weight savings and razor-sharp handling. Its lightweight construction and rigidity directly benefited its racing performance, contributing to successful motorsport campaigns.
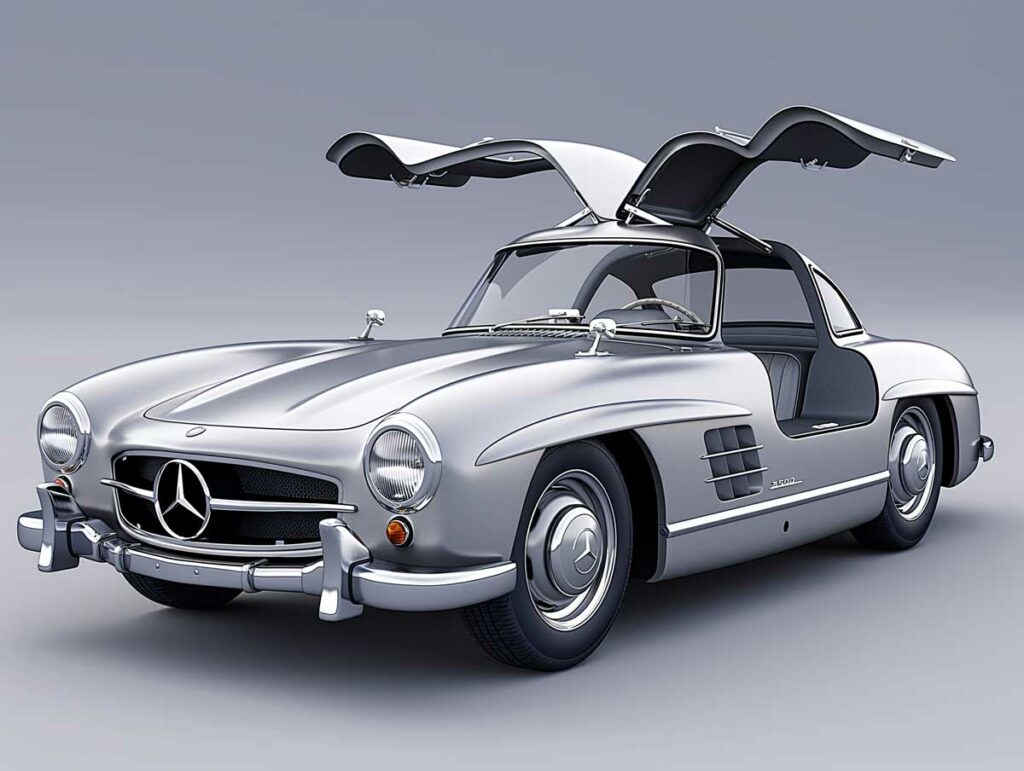
Enduring Legacy and Far-Reaching Impact
The 300SL’s space frame was not just a design choice but a game-changer in automotive chassis engineering. Its concept of combining lightweight construction with exceptional rigidity through geometric triangulation quickly became the standard for high-performance and racing cars, leaving an indelible mark on the industry.
From the Lotus Elite in 1957 to modern supercars, the tubular frame concept pioneered by Mercedes endures over half a century later. Even the iconic gullwing doors were a byproduct of the 300SL’s innovative chassis architecture. The Ferrari 250 GTO, one of the most iconic sports cars of the 1960s, employed a tubular frame chassis that contributed to its exceptional handling and race-winning performance. The McLaren F1, a legendary supercar of the 1990s, utilised a sophisticated tubular frame made of lightweight aluminium and magnesium, providing an incredible stiffness-to-weight ratio that enabled its remarkable performance. These examples demonstrate the lasting impact of the 300SL’s groundbreaking design on the automotive world.
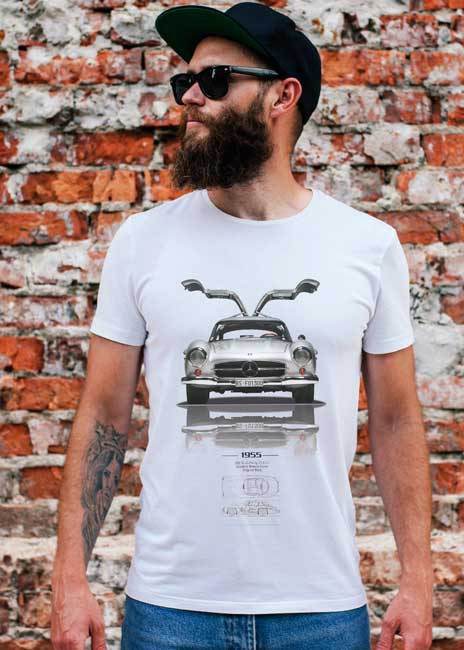
Own a Piece of this Racing Legend!
Grab your Mercedes-Benz 300SL T-Shirt from Original Race Australia today
Beyond the Realm of Supercars
The 300SL’s space frame didn’t just influence high-performance machines; its structural efficiency prompted mainstream automakers to adopt similar designs for affordable sports cars like the Lotus Elan.
As computer-aided design and manufacturing advanced, tubular chassis construction became increasingly sophisticated. It integrated crash structures and reinforced cockpit cells to meet stringent safety regulations. The tubular frame’s design ensures that it remains strong and rigid even under extreme conditions, providing high safety for the driver and passengers.
A Profound Philosophical Shift
The space frame of the 300SL was more than just a technical achievement; it marked a significant philosophical change in automotive engineering. It emphasised groundbreaking lightweight design over traditional manufacturing methods, completely transforming vehicle structures by reimagining chassis construction based on the fundamental principles of physics and materials science. This bold and characteristic approach, synonymous with Mercedes-Benz, continues to influence future generations of engineers and shape the direction of automotive design.
Conclusion
The Mercedes-Benz 300SL‘s tubular space frame was a groundbreaking feat of engineering that left an indelible mark on automotive history. Its principles of geometric reinforcement for stiffness and weight optimisation remain the foundation for modern, resilient, yet lightweight chassis construction.
The ingenuity and paradigm shift embodied by the 300SL’s tubular frame continues to influence racing technology and supercar engineering more than half a century later, cementing its status as a true engineering marvel. As automotive designers and engineers push the boundaries of performance and efficiency, the lessons learned from the 300SL’s revolutionary chassis will undoubtedly shape the vehicles of tomorrow.